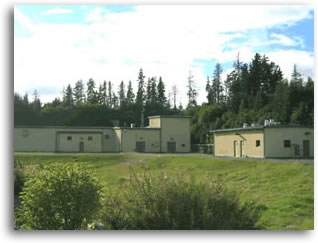
City of Homer, Public Works Department - Homer, Alaska
First municipal VBR system in the USA
Project Description: The Homer, Alaska wastewater treatment facility is the first municipal VBR sewage system in the USA. The town of Homer is located on the tip of the Kenai Peninsula “where the road meets the sea”. The permanent population of about 4,000 host some 20,000 annually, attracted by superb scenery and wildlife.
The VBR (effluent) plant was commissioned in 1991, and won the 1993 AWWA Large Plant of the Year award for the State of Alaska. The plant has produced specification or better effluent since commissioning, and upon start-up it successfully passed a one-year performance certification program for the EPA. During this program, the plant achieved an average effluent quality 33% below discharge specifications. Effluent quality is vital in this plant, as it discharges to the ecologically sensitive marine reserve of Kachemak Bay. “Our receiving water isn’t as clean as the [treated] water we’re putting into it. In fact, we’re upgrading the quality of Kachemak Bay” – Jim Hobbs, Wastewater Superintendent, City of Homer.
The small footprint of the VBR (effluent) plant allowed full enclosure in a 9,350 ft2 (870 m2) building, which also contains the head works, aerobic sludge digesters, and ultraviolet disinfection. Secondary treatment occurs in twin deep shafts 30 inches (.76 m) in diameter by 500 feet (152 m) deep, aerated by a single 40 hp (30 kW) rotary screw compressor. Two flotation clarifiers separate mixed liquor from the treated effluent.
Influent Design Flow: 880,000 US gallons per day (3332 m3/day)
Influent Design Conditions: 224 mg/L BOD, 316 mg/L TSS (9,900 population equivalent)
Effluent Standards: ≤ 30 mg/L BOD, ≤ 30 mg/L TSS
Effluent Achieved: < 10 mg/L BOD, < 15 mg/L TSS
*NORAM Biosystems Technology
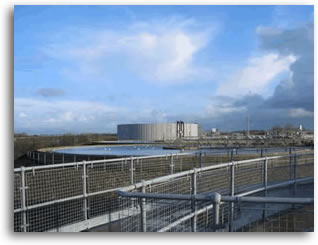 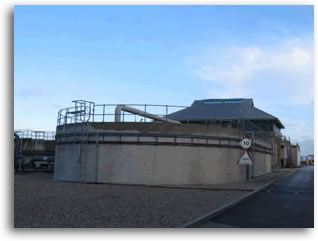
Northwest Water Authority - Southport, UK
Municipal Wastewater Treatment Facility
Project Description: Commissioned in 1996, the Southport, UK wastewater treatment facility is the largest municipal Deep Shaft system in the UK. This Deep Shaft system (a predecessor design to the VBR process) discharges treated effluent into an ecologically sensitive estuary, which is teeming with wildlife.
Due to the plant’s close proximity to an estuary and a very high ground water table in the area, flowing sands were encountered during shaft drilling. As a result, special drilling techniques were required to develop the shafts. A series of boreholes were sunk in a ring around the locations of the 2 future shafts. These boreholes were used to freeze the ground, creating a frozen collar in the ground. Drilling was then able to continue using conventional drilling techniques.
This vertical treatment plant handles domestic wastewater in the region with some light industrial loading as well. Unit processes in this facility include head works, anaerobic sludge digesters, and ultraviolet disinfection. Secondary treatment occurs in twin deep shafts 20 feet (6 m) in diameter by 350 feet (107 m) deep. A bank of rotary screw compressors aerate the shafts. Two large circular sedimentation clarifiers separate mixed liquor from the treated effluent before disinfection and discharge.
Influent Design Flow: 13.5 million US gallons per day (51,000 m3/day)
Influent Design Conditions: 222 mg/L BOD, 200 mg/L TSS (180,000 population equivalent)
Effluent Standards: ≤ 30 mg/L BOD, ≤ 30 mg/L TSS
Effluent Achieved: < 15 mg/L BOD, < 15 mg/L TSS
*NORAM Biosystems Technology
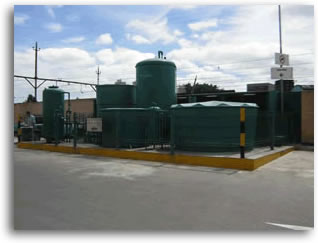 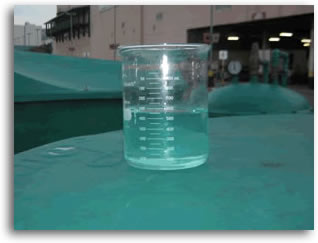
ABC Plaza Mall - Santo Andre City - São Paulo, Brazil
Municipal Wastewater Treatment for Water Reuse
Commissioning Date: January, 2008
Project Description: The ABC Plaza shopping mall, located just outside São Paulo, Brazil, has recently commissioned a new VBR wastewater treatment facility, using technology owned by Vancouver based Noram Engineering and Constructors Ltd. (www.noram-eng.com). A Brazilian Licensee of the VBR process, General Water SA, has completed construction and commenced a 20-yr operating contract.
The ABC Plaza Mall has a “population” of about 45,000 people/day. It has 300 stores and 63,000 square meters. The plant footprint is extremely small, with just a 45-centimeter diameter shaft treating the highly variable daily organic loading and hydraulic flow patterns found in the shopping center.
The VBR (effluent) plant achieves secondary treatment in a single shaft, followed by a flotation clarifier that separates mixed liquor from the treated effluent. Tertiary sand filters are used to further treat the effluent to high quality reuse water specifications. Treated water is reused in the mall cooling system, for irrigation, and in sanitary discharge service to decrease the use of potable water. Every drop of the treated effluent is reused at the site.
Influent Design Flow: 200 m3/day
Influent Design Conditions: 550 mg/L BOD, 400 mg/L TSS (1500 population equivalent)
Effluent Standards: ≤ 10 mg/L BOD, ≤ 10 mg/L TSS
Effluent Achieved: < 5 mg/L BOD, < 5 mg/L TSS
*NORAM Biosystems Technology
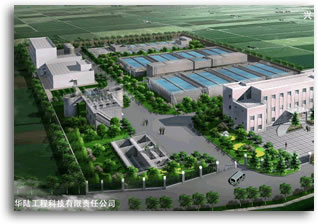
City of Xingping & Shenzhen Blue Phoenix Industrial Development Ltd.- Xingping, Shaanxi, China
Municipal Wastewater Treatment Facility
Commissioning Date: April, 2009
Project Description: The Xingping VBR system is completed construction in April 2009, and quickly achieved all process acceptance testing by the Chinese Environmental Bureau. This is the first VBR treatment facility in China, and ultimately constitutes the first phase of a grander scheme, as the VBR (effluent) system will be mirrored at the site in the future. Treated effluent will be discharged to the Wei River, and as such must meet a very high standard for treatment. The Xingping wastewater treatment plant has been designed to treat both domestic wastewater from the City of Xingping, as well as industrial wastewater inputs from a neighboring fertilizer production facility. The fertilizer plant is significantly increases the ammonia content in the wastewater, necessitating the inclusion of a complete BNR (biological nutrient removal) design to target the ammonia residuals. Long term planning calls for use of the treated water for irrigation of neighboring farm land. Unit processes in this VBR facility include head works (screening and degritting), sludge dewatering, and BAFs (biological aerated filters). Secondary treatment occurs in twin vertical shafts 3.2 meters (10.5 ft) in diameter by 92 meters (302 ft) deep. A bank of rotary screw compressors aerate the shafts and 16 custom designed rectangular clarifiers separate mixed liquor from the treated effluent.
Influent Design Flow: 50,000 m3/day (13.2 million US gallons per day)
Influent Design Conditions: 220 mg/L BOD, 220 mg/L TSS (130,000 population equivalent)
Effluent Standards: ≤ 25 mg/L BOD, ≤ 30 mg/L TSS, ≤ 100 mg/L COD
Effluent Achieved: < 10 mg/L BOD, < 10 mg/L TSS, < 50 mg/L COD
*NORAM Biosystems Technology
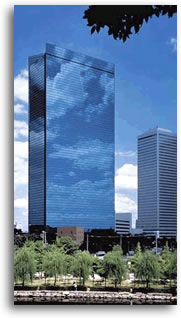 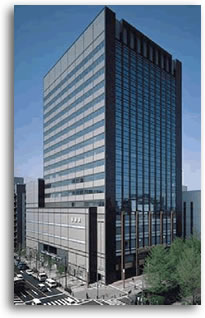 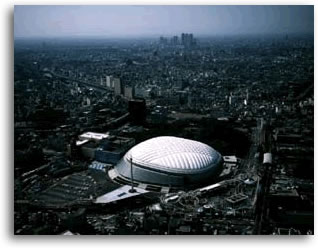
(Hilton, Mitsui, Mitsubishi) - Varied throughout Tokyo & Japan
Domestic Wastewater Treatment with some Water Reuse
Commissioning Date: 1985 - 1991
Project Description: Early Licensee’s of the Deep Shaft process (a predecessor to today’s VBR process) were very active in the Japanese market. Multi-national companies such as Kubota, Hitachi, and Mitsubishi were all licensee’s of the process, and built a substantial number of facilities through the 1980’s and into the 1990’s.
Companies in Japan were quick to adopt vertical aeration shaft technology, as they were offered significant government tax incentives to reduce their energy footprint. The Deep Shaft process was one of a handful of technologies recognized by Japanese authorities for its potential to minimize energy consumption through improved aeration efficiency.
Domestic sewage treatment plants in Japan vary in size, ranging from a population equivalent of 1,000 to 30,000 people. The pictures above show Tokyo Dome (Baseball Stadium), the Hamacho Centre Building, and the Mitsui-Hakozaki Building. In all of the office building designs, the plant footprint is extremely small, usually with a single shaft located in the basement of the building. Many of the buildings reuse the treated water in the air conditioning systems, atoning to the high quality of the effluent that is discharged.
Influent Design Flow: 136 - 10,000 m3/day (36,000 gpd - 2.7 MGD)
Influent Design Conditions: Varied BOD & TSS (1000 - 30,000 population equivalent)
Effluent Standards: ≤ 30 mg/L BOD, ≤ 30 mg/L TSS
Effluent Achieved: < 10 mg/L BOD, < 10 mg/L TSS
*NORAM Biosystems Technology
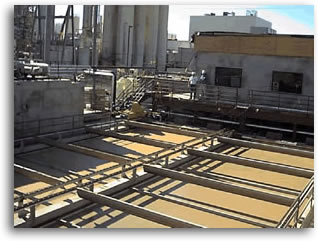 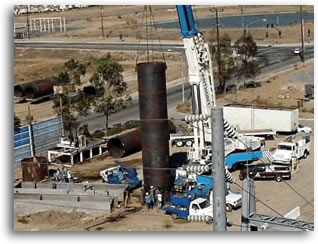
Golden Cheese Company of California - Corona, California, USA
Industrial Wastewater Pre-Treatment Facility
Commissioning Date: November, 2000
Project Description: The Golden Cheese wastewater treatment plant is the largest VBR wastewater system in North America. The system treats high-strength cheese processing wastewater from the largest cheese producer in the US, with a rated capacity of 16,000 lbs of BOD per day, pH swings between 4-11, and spike loadings that pushed the peaking factor as high as 5x the plant’s design capacity.
The VBR wastewater system not only resulted in significant capital and operating cost savings, it treats this high organic load on a very small footprint – roughly 1100 m2, which amounts to approximately 20% of the space requirement of a conventional technology. The minimal footprint made the process an ideal fit for the expanding dairy. Secondary treatment occurs in twin deep shafts 9 feet (2.8 m) in diameter by 308 feet (97 m) deep, and two flotation clarifiers separate mixed liquor from the treated effluent. The plant was started up ahead of schedule, and met all process design requirements upon plant commissioning.
NORAM provided the following on a fixed price basis as part of a process performance based contract: VBR process design, engineering, equipment procurement, building design criteria, construction supervision, process guarantees, and plant commissioning.
Influent Design Flow: 700,000 US gallons per day (2650 m3/day)
Influent Design Conditions: 2700 mg/L BOD, 700 mg/L TSS (135,000 population equivalent)
Effluent Standards: ≤ 250 mg/L BOD, ≤ 250 mg/L TSS
Effluent Achieved: < 50 mg/L BOD, < 50 mg/L TSS
*NORAM Biosystems Technology
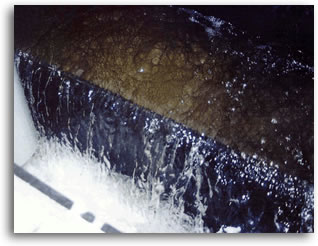
Chevron Canada Ltd. - Burnaby, BC, Canada
Industrial Wastewater Treatment Facility
Commissioning Date: October, 1996
Project Description: The Chevron Canada Ltd. petroleum refinery at Burnaby, British Columbia, Canada produces approximately 9500 m3/day (60,000 barrels per day) of gasoline, distillate fuel, and aviation fuel. A VBR system treats the wastewater from refining processes including crude desalting & other direct oil/water contacting. Process wastewater contains FOG (Free Oil and Grease), BTEX (Benzene, Toluene, Ethyl Benzene, Xylene), MTBE (Methyl tert-Butyl Ether), NH3 (Ammonia), and H2S (Hydrogen Sulphide).
This VBR (effluent) plant was commissioned in 1996, and honoured with the British Columbia Water & Waste Association Industrial Pollution Control Award in 1997. The system is a fully “integrated” design, treating the wastewater, sludge, and air streams within the process. The plant has proved robust against swings in influent flow, strength and pH, considerably outside the design basis. In particular, the buffering capacity of the reactor has proved truly remarkable, as large caustic spills have been absorbed by the effluent treatment system with no action from plant personnel.
The VBR plant at Chevron occupies 700m2 (7500ft2) and operates on 56kW (75hp) at peak load. By comparison, a traditional aerobic system would require a land area of 3500m2 and consume 112kW – approximately five times the land space requirement and double the operating cost.
Influent Design Flow: 700,000 US gallons per day (2650 m3/day)
Influent Design Conditions: 250 mg/L BOD, 500 mg/L COD (9,000 population equivalent)
Effluent Standards: ≤ 100 mg/L BOD, ≤ 40 mg/L TSS
Effluent Achieved: < 5 mg/L BOD, < 5 mg/L TSS, LC50 = 100%
*NORAM Biosystems Technology
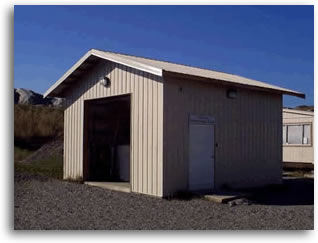 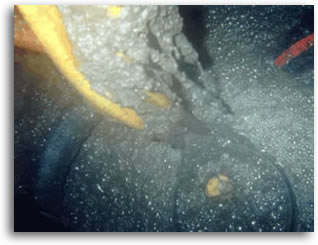
King County Department of Natural Resources - Seattle, WA South Treatment Plant, Renton, WA
Mixed Primary and Secondary Solids Digestion
Commissioning Date: January, 1998
Project Description: Through sponsorship by the King County Department of Natural Resources, a facility was constructed and operated to demonstrate the performance of the VBR process. TAP (Technology Assessment Program) evaluated digestion technology alternatives that provided: 1. A smaller process footprint for sludge digestion facilities; 2. Better control of odorous emissions; 3. Reduced biosolids hauling truck traffic.
The VBR facility consists of a 0.5 meter (20-inch) diameter by 107 meter (350-foot) deep reactor with a head tank that provides 21 m3 (5,535 gallons) of processing capacity. The facility can process 318 kg (700 lbs) of volatile solids per day or the equivalent to solids from a treatment plant processing 1893 m3/day (0.5 MGD) of sewage, or a 5000 population equivalent.
The VBR process was demonstrated to produce a Class A biosolids product at a 3 to 4-day detention time (with 38 to 43% volatile solids reduction 60°C). Oxygen transfer efficiency was measured at 30 to 62% (despite sludge concentrations averaging 40,000 mg/L and temperatures reaching 65°C). The system generates excess heat which is recoverable as for low grade heat applications and eliminates nuisance odors that are typically associated with conventional ATAD systems. The product dewaters significantly better than anaerobic digestion products, producing thicker cake solids with lower polymer requirements.
Influent Design Flow: 3.5 - 7.0 m3/day
Influent Design Conditions: 60 : 40% - primary : secondary sludge, 65,000 mg/L TS, 80% VS content
Biosolids Standards: > 38% VS Reduction @ 4-day HRT, 7 log pathogen reduction
Biosolids Achieved: Class A Biosolids (EPA 503 regulations, Alternative 1)
*NORAM Biosystems Technology
|